-
Global
-
Africa
-
Asia Pacific
-
Europe
-
Latin America
-
Middle East
-
North America
- |
- Partners
- |
-
Currency:Localize your Content
You can set your preferred currency for this account.
Choose a Currency
Currency- CHOOSE YOUR CURRENCY
Update Currency
Changing Currency will cause your current cart to be deleted. Click OK to proceed.
To Keep your current cart, click CLOSE and then save your cart before changing currency.
-
Select Account
Switching accounts will update the product catalog available to you. When switching accounts, your current cart will not move to the new account you select. Your current cart will be available if you log back into this account again.
Account# Account Name City Zip/Post Code CANCELPROCEEDMy Account
-
Support
- View All Productivity Solutions
- Warranties
- Patents
- Global Locations
- Technical Support
- Discontinued Products
- Quality Program and Environmental Compliance
- Return Material Authorization (RMA)
- Legal Documents
- Product Certification
- Software Downloads
- Cyber Security Notifications
- Case Studies and Success Stories
- View All Sensing Solutions
- Sales Contact Form
- Technical Support
- Certificates
- eCOM Portal
- Distributor Inventory
- Return Material Authorization (Test & Measurement)
- Return Material Authorization (Citytech)
- Return Material Authorization (EnviteC)
- Legal Documents
- Intelligent Life Care
- Return Material Authorization (ILC)
-
Global
-
Africa
-
Asia Pacific
-
Europe
-
Latin America
-
Middle East
-
North America
- |
- Partners
- |
You are browsing the product catalog for
You are viewing the overview and resources for
- News & Events
- Featured stories
- Real Examples of Increased Warehouse Profits with Industry 4.0 | Honeywell Intelligrated
Real Examples of Increased Productivity, Efficiency and Profits with Industry 4.0
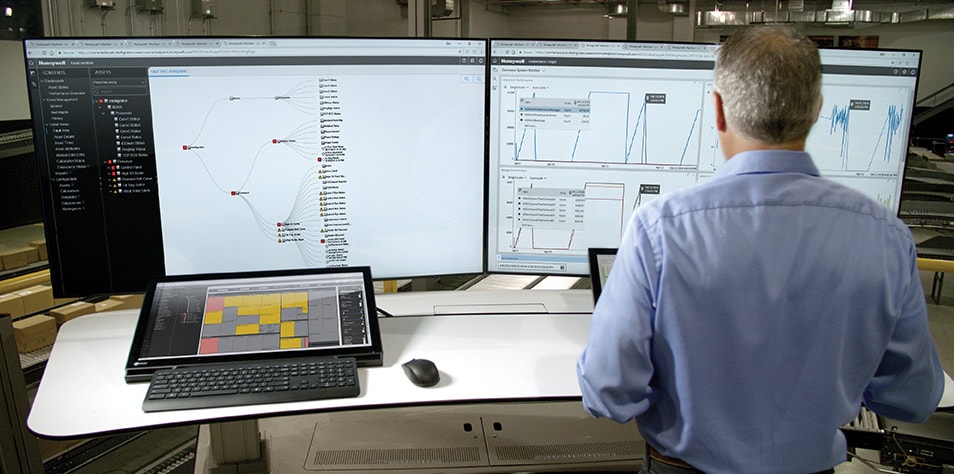
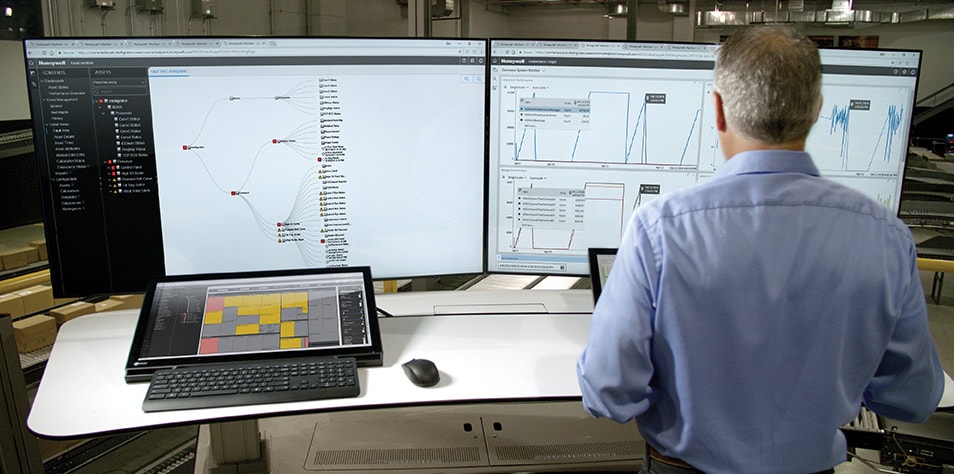
Real Examples of Increased Warehouse Profits with Industry 4.0 | Honeywell Intelligrated
William Leet
January 12, 2021
In a recent webinar moderated by Bob Trebilcock of Modern Materials Handling, “Industry 4.0: Real Cases of Productivity, Efficiency and Profits,” we detailed one customer’s experience with Honeywell Intelligrated’s Connected Assets offering — applied to their existing sortation system — which uncovered significant savings in terms of productivity and efficiency as well as ways to increase profitability. The following is an overview of the webinar. For detailed examples of customer cost savings and the calculations we used, you can watch the webinar by clicking the link above or you may contact us for an explanation of our findings.
Today’s distribution and fulfillment (D&F) centers have been running at peak levels for months due to COVID-19. And with little (or in some cases, zero) time for maintenance, they face an increased risk of mechanical failures — especially with a widespread utilization of legacy systems.
In previous years, any mechanical downtime was simply offset by increasing staff or running extra shifts to overcome lost productivity. But in addition to already running machinery at peak levels, distribution centers (DCs) are experiencing shorter delivery windows, extended lead times and record-breaking shipping volumes. Thus, playing catch-up is not a viable solution.
Beyond the increased risk and limited production windows, facilities are also experiencing labor shortages, retiring of skilled workers, and travel and visitor restrictions. These factors reduce the pool of maintenance technicians available — potentially delaying repairs, lengthening overall downtime, and increasing the difficulty of repair.
Smart distribution center operators should be asking themselves:
- By running my DC assets harder and with little to no maintenance, what level of risk am I exposing myself to? And how is it increasing?
- Downtime is progressively disruptive and expensive, but how much downtime do I currently have? And what can I save by reducing it?
- It’s increasingly difficult to find people to repair and recover systems. What can I do to better maintain my equipment?
The answers might seem impossible to obtain, but it can be done. In fact, these questions are the same ones we helped one of our customers answer over a 12-month period by employing Industry 4.0: the combination of machine-to-machine communication and the industrial internet of things (IIoT) to increase automation, communication, self-monitoring and analysis.
To answer our previous questions, we must first create several hypotheses:
- If customers are not using IIoT, then they are exposed to unnecessary and considerable risks. And those risks increase exponentially.
- If customers use IIoT, they can significantly reduce their current cost of downtime and future downtime costs by at least 30%.
- If customers evolve from a time-based maintenance program to one that is condition-based, they can minimize troubleshooting, increase efficiency, and balance their costs versus risks.
To test our hypotheses, we installed several sensor types on two sorters at a retail distribution center with 20% of its throughput operating as “consumer direct”. Over the 12-month project, we anticipated identifying 10 potential work-stoppage incidents before they occurred. We found seven incidents with estimated costs varying between $4,000 and $18,000 per event, for a total estimated savings of $70,000 in unplanned downtime. These incidents were identified through increased vibration detected by the installed sensors and followed the typical asset lifecycle (i.e., as an asset ages, the likelihood of failure increases).
In addition to the potential savings from averting unplanned downtime, there is also a theoretical productivity reallocation opportunity by reducing the number of planned maintenance events. For example, a site with three maintenance technicians can utilize system data to avoid unnecessary walkthroughs (an estimated value of $3,000) and walkthrough-related activities (an estimated value of $3,840) as well as using that data to pinpoint where to troubleshoot (an estimated value of $9,000) for a total of $15,000 to $16,000 in productivity reallocation per year.
There is an additional benefit of connecting assets. Instead of manually collecting datapoints from walkthroughs, the data collection is not only automated but continuous. This provides a much more comprehensive view of the system’s health and circumvents the need for a human to sort and calculate the data. Compared to a person collecting the data, Industry 4.0 can conservatively provide a labor savings of more than $10,000 per year. It is important to note this estimation is only for one person; it could increase, as it does not include operational savings.
Digital Transformation = Real Business Results
During the 12-month data collection period, we estimate Industry 4.0 had the following business impacts for our customer:
- $50,000+ reduction in risk
- $70,000 reduction in the cost of downtime
- $15,000 savings in maintenance
- $25,000 increased productivity
- $15,000 unexpected savings
Data Drives Transparency
If you’re thinking about implementing Industry 4.0, our team can help you to decide if it is right for you. We’ll work with you to define expected outcomes, create a data strategy, establish building blocks, implement the plan, and deliver outcomes.
Be sure to contact us today as Industry 4.0 adoption continues to accelerate; we are on the cusp of its widespread implementation. The sooner you determine if Industry 4.0 is right for you, the faster you will be able to reap its benefits of operational efficiency, productivity and profitability.
To subscribe to our blog and receive exclusive communications and updates from Honeywell Intelligrated, click here.
Let's Connect!
Sign up to receive exclusive communications from Honeywell including product updates, technical information, new offerings, events and news, surveys, special offers, and related topics via telephone, email, and other forms of electronic communication.
Copyright © 2025 Honeywell International Inc
Maximum File Size
Maximum Files Exceeded
Due to inactivity you will be logged out in 000 seconds.
Maximum File Size
Maximum Files Exceeded
You cannot access this page as this product is not available in your country.