-
Global
-
Africa
-
Asia Pacific
-
Europe
-
Latin America
-
Middle East
-
North America
- |
- Partners
- |
-
Currency:Localize your Content
You can set your preferred currency for this account.
Choose a Currency
Currency- CHOOSE YOUR CURRENCY
Update Currency
Changing Currency will cause your current cart to be deleted. Click OK to proceed.
To Keep your current cart, click CLOSE and then save your cart before changing currency.
-
Select Account
Switching accounts will update the product catalog available to you. When switching accounts, your current cart will not move to the new account you select. Your current cart will be available if you log back into this account again.
Account# Account Name City Zip/Post Code CANCELPROCEEDMy Account
-
Support
- View All Productivity Solutions
- Warranties
- Patents
- Global Locations
- Technical Support
- Discontinued Products
- Quality Program and Environmental Compliance
- Return Material Authorization (RMA)
- Legal Documents
- Product Certification
- Software Downloads
- Cyber Security Notifications
- Case Studies and Success Stories
- View All Sensing Solutions
- Sales Contact Form
- Technical Support
- Certificates
- eCOM Portal
- Distributor Inventory
- Return Material Authorization (Test & Measurement)
- Return Material Authorization (Citytech)
- Return Material Authorization (EnviteC)
- Legal Documents
- Intelligent Life Care
- Return Material Authorization (ILC)
-
Global
-
Africa
-
Asia Pacific
-
Europe
-
Latin America
-
Middle East
-
North America
- |
- Partners
- |
You are browsing the product catalog for
You are viewing the overview and resources for
- News & Events
- Featured stories
- Honeywell Operational Intelligence Configuration Management Module Streamlines Remote Device Updates
Honeywell Operational Intelligence Configuration Management Module Streamlines Remote Device Updates
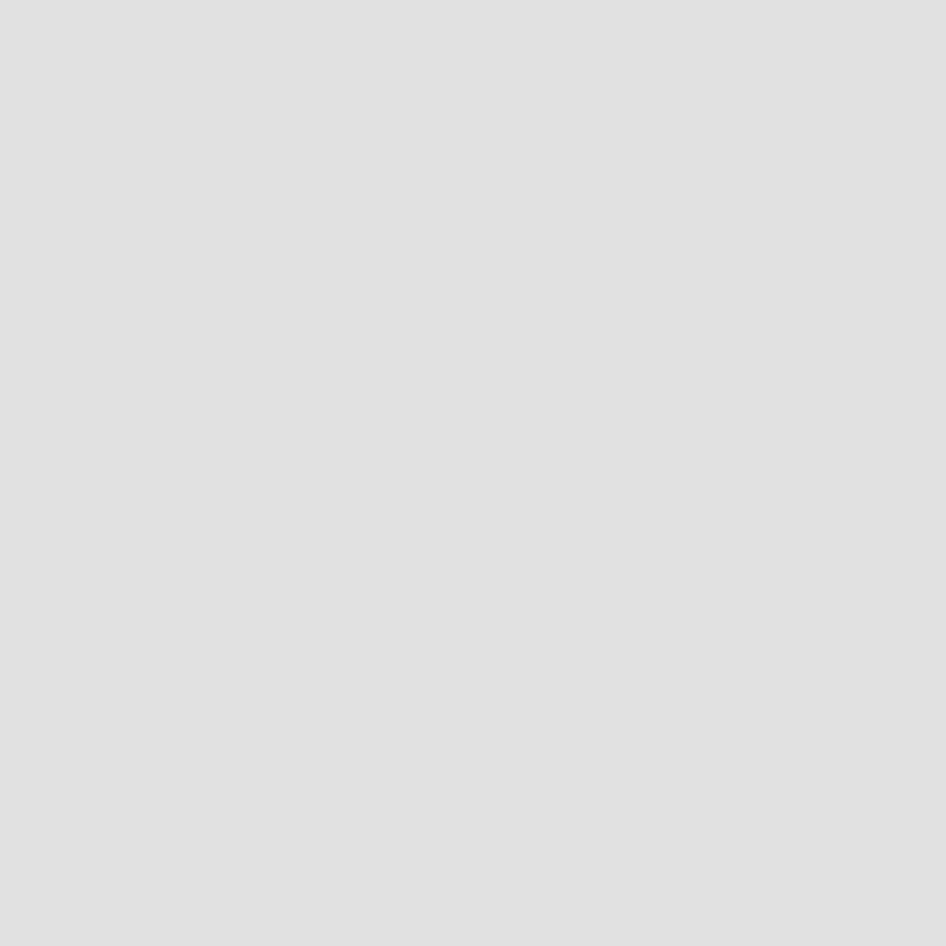
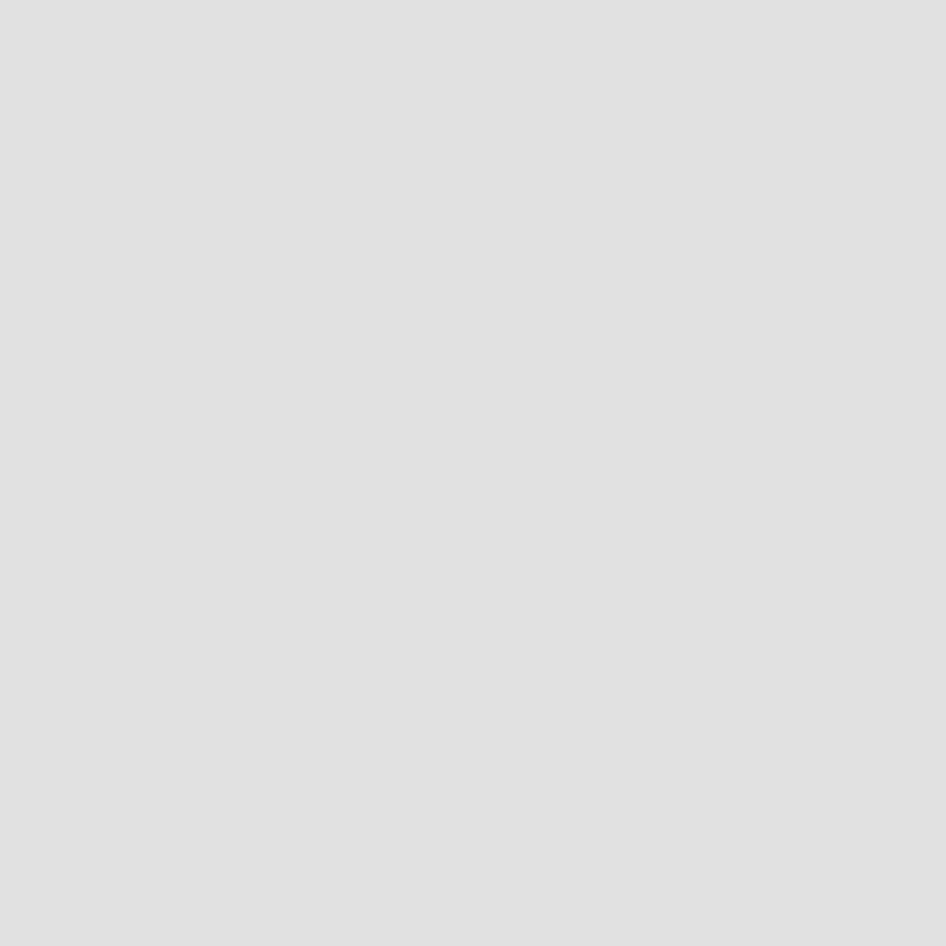
Honeywell Operational Intelligence Configuration Management Module Streamlines Remote Device Updates
Barry J. Ewell
December 19, 2019
This is a five-part series looking at how Honeywell is revolutionizing IT asset and service management with Operational Intelligence. Operational Intelligence includes four modules to give you a robust tool to manage and optimize assets across your locations throughout the operational asset lifecycle. These include: 1) Service Management, 2) Performance Management, 3) Configuration Management, and 4) Worker Performance. Part 3 will introduce the Configuration Management module.
Across the supply chain, organizations deploy fleets of mobile devices made up of assets from multiple manufacturers – ruggedized mobile computers, tablets, barcode scanners, and printers. Each device comes with its own operating system, software, contracts, agreements, and repair processes that must be carefully managed. Many of these devices can collect rich telemetry and event data that can be used to provide actionable insights into how devices are used, how to decrease operational costs, and how to improve productivity. Sadly, organizations are challenged in accessing these insights because they are using separate tools and aggregating the information with spreadsheets and in-house developed tools.
Operational Intelligence Overview
Honeywell Operational Intelligence solves these needs and problems by providing IT and site leaders and services providers a centralized, cloud-based platform to manage the complete lifecycle of their assets. Operational Intelligence aggregates lifecycle and workflow information into a single flexible tool to capture data, enforce processes, and provide visibility across the entire device workflow for your heterogeneous environment. Operational Intelligence is also capable of communicating with Honeywell devices to gather deep metric and telemetry data; provide software, configuration, OS, and firmware updates to the devices; and track indoor device location.
Operational Intelligence is a powerful analysis software engine that provides dashboards to support your troubleshooting efforts. At Honeywell, we believe in the power of intelligence and design products to give you more of it. Over the last several years, Honeywell has been systematically adding powerful “self-analyzing” toolsets to all of our hardware products. These embedded tools are capable of methodically capturing hundreds of performance data points from our devices as they are being used in your operations. When this data is compiled and analyzed, it opens amazing insights into many problems common to AIDC technology users.
Operational Intelligence includes four modules to give you a robust tool to manage and optimize assets across your locations throughout the operational asset lifecycle. These include:
- Service Management: As a vendor-agnostic solution, systematically standardize, manage, and optimize the process of servicing your IT assets.
- Performance Management: Track, analyze, and report on the operational performance of your IT assets. Remotely download software and configurations.
- Configuration Management: Reduce time spent on individual device updates and security risks by keeping devices automatically updated.
- Worker Performance: Analyze worker performance and workflow efficiencies by tracking device and application use.
A Closer Look at Configuration Management Module
Operational Intelligence reduces time spent on individual device updates and security risks by keeping devices automatically updated. This is possible because Operational Intelligence supports Honeywell’s Mobility Edge™ platform. With the Configuration Management module, you gain access to:
- Software Updates. Remotely update your IT assets’ operating system, firmware, and security software to reduce cybersecurity risks as well as time spent on individual device updates.
- Configuration Updates. Remotely configure your IT assets software systems and applications to be eligible for OS vendor standard support.
- Remote Control. Remotely troubleshoot device issues and test real-time configuration updates.
Some of the module highlights include:
- Pushing out new software updates
- Pushing out new device configuration files
- Remote device control to support advanced troubleshooting
Mobility Edge overview
Mobility Edge is based upon extensive research gathered from Honeywell’s global community of customers from a range of technologies. Honeywell recognized that businesses wanted a unified hardware and software platform for all form factors – one that allowed for rapid deployments, robust performance, and adaptability to changing needs.
We completely rethought our approach to meeting the challenges of supporting a mobile workforce, and Mobility Edge was the answer. This unified, dynamic platform for mobile computing is designed to:
- Accelerate deployments
- Optimize business performance
- Extend lifecycle
- Strengthen security
Honeywell Mobility Edge devices built on this common hardware and software platform are easier and less costly to deploy and manage and have longer lifecycles than similar competitive devices.
Mobility Edge devices feature a common hardware System On Module, or SOM, which is a single, certified module that includes the device’s CPU, memory, WWAN (in selected devices), WLAN, Bluetooth®, near-field communication (NFC), and Zigbee (in selected devices). They also feature a common OS software image and a common software ecosystem, which includes not only Honeywell software, but also software from Honeywell-approved independent software vendors (ISVs).
Having a common SOM and OS software image provides flexibility and reduces costs for businesses to deploy additional device form factors, because there are no added development or certification costs. Companies can validate all their mobile devices, use cases, and software once, and then deploy across multiple devices in multiple form factors, more rapidly and at a lower cost than typical mobile deployments.
Businesses wishing to extend product lifecycle and gain a better return on their technology investment will be assured by the fact that Mobility Edge platform devices can be upgraded through Android™ R. Honeywell also provides critical security updates for up to two years past Google’s last security patch through its Sentinel service, giving customers a product lifecycle through at least 2027.
Honeywell is deeply committed to the longevity and quality of the Mobility Edge platform. The current family of devices includes the CT40, CT60, CN80, CK65, and Thor™ VM1A, all running on Mobility Edge. More devices are in process for future release. A brief overview of each device follows:
- CN80 mobile computer, an ultra-rugged device for warehouse, manufacturing, and transportation and logistics environments. The most durable handheld Honeywell has ever made, it features both keypad and large touchscreen interface for quick, efficient data entry.
- CT60 mobile computer, a rugged, versatile business tool for highly mobile frontline workers in scan-intensive workflows in pickup and delivery, DSD, and parcel post. It offers a long-lasting battery, high-performance scanning, and exceptional durability and reliability.
- CT40 mobile computer, a full-touch, five-inch display device designed for retail, hospitality, and light field mobility environments. It’s an intuitive, compact productivity tool optimized for hours of comfortable use.
- CK65 mobile computer, a rugged, flexible solution for warehouse and manufacturing environments, with both touchscreen and keypad data input options for quick data entry and enhanced scanning read ranges of up to 15.2 m (50 ft).
- Thor™ VM1A, the world’s top-selling vehicle-mounted computer, upgraded to Mobility Edge. Hits the sweet spot of overall size, display size, and keypad. The Smart Dock enables use on multiple vehicles and reduces support and maintenance costs. A field-replaceable front panel minimizes downtime.
Accelerate deployments with Mobility Edge and Operational Intelligence
At Honeywell, we have the solution to slow, labor-intensive implementations: rapid deployment on devices built on Mobility Edge. You can validate all your mobile devices, use cases, and software once, and then deploy across multiple devices in multiple form factors – faster, easier, and at lower cost.
For example, if you are a retailer, you may have a myriad of devices that are optimized for different environments such as the front of the store or backroom, and others for the distribution or fulfillment center. With Mobility Edge, your one-time investment in setup, deployment, and provisioning is reusable across all devices.
Quickly configure and deploy devices into the hands of mobile workers with a comprehensive provisioning toolkit including:
- Enterprise Provisioner – Allows you to create barcodes that contain provisioning instructions and configuration settings that can easily be scanned by the device operator to provision their device and make it ready for use – quickly, reliably, and with no error-prone manual entry of settings.
- Setup Wizard – Enables you to quickly set up and configure devices by scanning barcodes, reading QR codes, or tapping an NFC tag.
- Staging Hub – Allows you to push a bundle of applications and configuration settings to your entire fleet of devices. Staging Hub allows you to see all your devices within the network from a central console and push bundles to each device.
- Secure Provisioning – Part of the architecture of the product, Secure Provisioning uses cryptographic methods to ensure that each device is securely set up and unalterable by a third-party intrusion.
- Android™ Zero-Touch Enrollment – Allows IT to deploy corporate-owned devices in bulk without having to manually set up each device. Users just open the box and start using the device with management, apps, and configurations all set.
Manage mobile device cybersecurity risks
Currently about 71% of Android devices are not running the latest security patch. Being able to manage the operational lifecycle of your mobile device security is a very important aspect of managing those mobile devices.
You will know the security profile and the security risk based on updates/patches that are available from Google. Gain the ability to manage and control device profiles by pushing updates and removing and adding software.
Honeywell has a deep institutional and cultural focus on security across multiple domains. We invest over $50 million annually in cybersecurity and employ 300+ dedicated security professionals who are focused on protecting our customers.
We design security into our products, policies, and processes. The best way to ensure that you have a secure device is to make sure that you are using the most recent version of the operating system and up-to-date security patches. We provide a regular security patch cadence for Mobility Edge devices of at least every 90 days, and often as frequently as every 30 days.
Our security built-in, design-to-delivery process has a strong emphasis on programming security into products to anticipate and mitigate risk. We do this by embedding deep domain knowledge of industry-leading security practices throughout our full design and development process to ensure our solutions are as secure as possible from the start. We also make our solutions as free of vulnerabilities to attack as possible through such measures as continuous testing, authentication safeguards, and adherence to best programming practices. And, this isn’t anything new for Honeywell. We have had over 1,000 global engagements since 2006, and are the provider of managed security services for over 350 industrial sites. To continue our focus and lead the way in the industry, we put in place the industry’s first Cybersecurity Risk Manager and developed strategic partnerships with leading cybersecurity product vendors.
Conclusion
Honeywell Operational Intelligence is a cloud-based platform to manage the complete lifecycle of your assets. Operational Intelligence aggregates lifecycle and workflow information into a single, flexible tool to capture data, enforce processes, and provide visibility across the entire device workflow for your heterogeneous environment. Operational Intelligence is also capable of communicating with Honeywell devices to gather deep metric and telemetry data; provide software, configuration, OS, and firmware updates to the devices; and track indoor device location.
Operational Intelligence is a powerful analysis software engine that provides dashboards to support your troubleshooting efforts. At Honeywell, we believe in the power of intelligence and design products to give you more of it. That’s why we have been systematically adding powerful “self-analyzing” toolsets to all of our hardware products. These embedded tools we call “Edge Intelligence” are capable of methodically capturing hundreds of performance data points from our devices as they are being used in your operations. When this data is compiled and analyzed, it opens amazing insights into many problems common to AIDC technology users.
Operational Intelligence delivers results that have been previously unattainable with any one solution. These include:
- Assign assets to unique departments and locations for accountability.
- Receive real-time status updates on assets returned for repair to reduce help desk status calls.
- Define self-service checklists to follow prior to RMA issuance to reduce NFF returns and create accountability.
- Simplify the RMA process by consolidating and standardizing the lifecycle management processes by digitizing your service and repair workflow, ensuring global consistency and simplifying the process for all employees.
- Control corporate shipping methods through automated integration to understand and reduce shipping costs.
- Minimize size of spare pools, reducing upfront capital expenditure.
- Properly allocate devices to locations and departments based on usage to improve productivity.
- Track connected mobile devices in operation and unconnected mobile devices through their service repair workflow and back into operations or spare pools to reduce lost devices.
- Reduce wasteful spend on unnecessary equipment purchases by analyzing device utilization and alerting supervisors to underutilized devices that could be relocated.
- Receive device lifecycle analytics to make informed decisions to refresh devices, spot reoccurring device issues, and identify individual problem devices.
- Track and locate devices to minimize lost devices.
- Minimize productivity loss with real-time notifications for printer jams and out-of-media and ink issues.
- Increase device uptime and availability by providing predictive notifications about pending maintenance needs or consumable replacements such as batteries, labels, printheads, and more.
- Track dropped and high-impact events on the devices to understand the care and use of the devices.
- Understand battery usage to drive behavior changes to extend the lifespan of batteries.
- Receive recommendations and make informed decisions regarding battery replacements based on health.
- Device OS and firmware update capabilities and versioning tracking so you can have visibility into security vulnerabilities and can patch devices to enforce compliance and mitigate risk.
- Integrated dashboards, KPIs, alerts, and notifications to provide device usage and productivity degradation events to improve utilization and productivity.
If you want to learn how Operational Intelligence can help you better manage your mobile assets, contact Honeywell today at https://www.honeywellaidc.com/solutions/workflow/operational-intelligence.
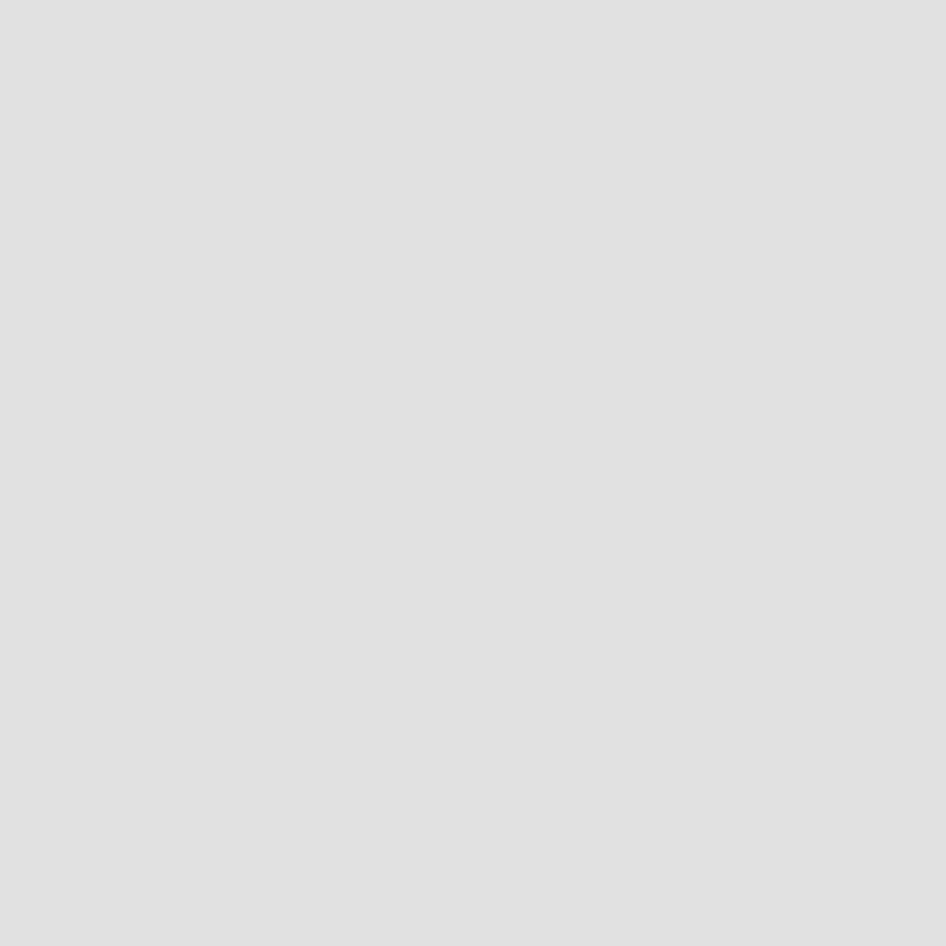
Barry J. Ewell is a Senior Content Marketing Communications Specialist for Honeywell Industrial Automation. He has been researching and writing on supply chain topics since 1991.
Let's Connect!
Sign up to receive exclusive communications from Honeywell including product updates, technical information, new offerings, events and news, surveys, special offers, and related topics via telephone, email, and other forms of electronic communication.
Copyright © 2025 Honeywell International Inc
Maximum File Size
Maximum Files Exceeded
Due to inactivity you will be logged out in 000 seconds.
Maximum File Size
Maximum Files Exceeded
You cannot access this page as this product is not available in your country.