-
Global
-
Africa
-
Asia Pacific
-
Europe
-
Latin America
-
Middle East
-
North America
- |
- Partners
- |
-
Currency:Localize your Content
You can set your preferred currency for this account.
Choose a Currency
Currency- CHOOSE YOUR CURRENCY
Update Currency
Changing Currency will cause your current cart to be deleted. Click OK to proceed.
To Keep your current cart, click CLOSE and then save your cart before changing currency.
-
Select Account
Switching accounts will update the product catalog available to you. When switching accounts, your current cart will not move to the new account you select. Your current cart will be available if you log back into this account again.
Account# Account Name City Zip/Post Code CANCELPROCEEDMy Account
-
Support
- View All Productivity Solutions
- Warranties
- Patents
- Global Locations
- Technical Support
- Discontinued Products
- Quality Program and Environmental Compliance
- Return Material Authorization (RMA)
- Legal Documents
- Product Certification
- Software Downloads
- Cyber Security Notifications
- Case Studies and Success Stories
-
Global
-
Africa
-
Asia Pacific
-
Europe
-
Latin America
-
Middle East
-
North America
- |
- Partners
- |
You are browsing the product catalog for
You are viewing the overview and resources for
- News & Events
- Featured stories
- Which Vertical Conveyor Is Best for Your Operations?
Which Vertical Conveyor Is Best for Your Operations?
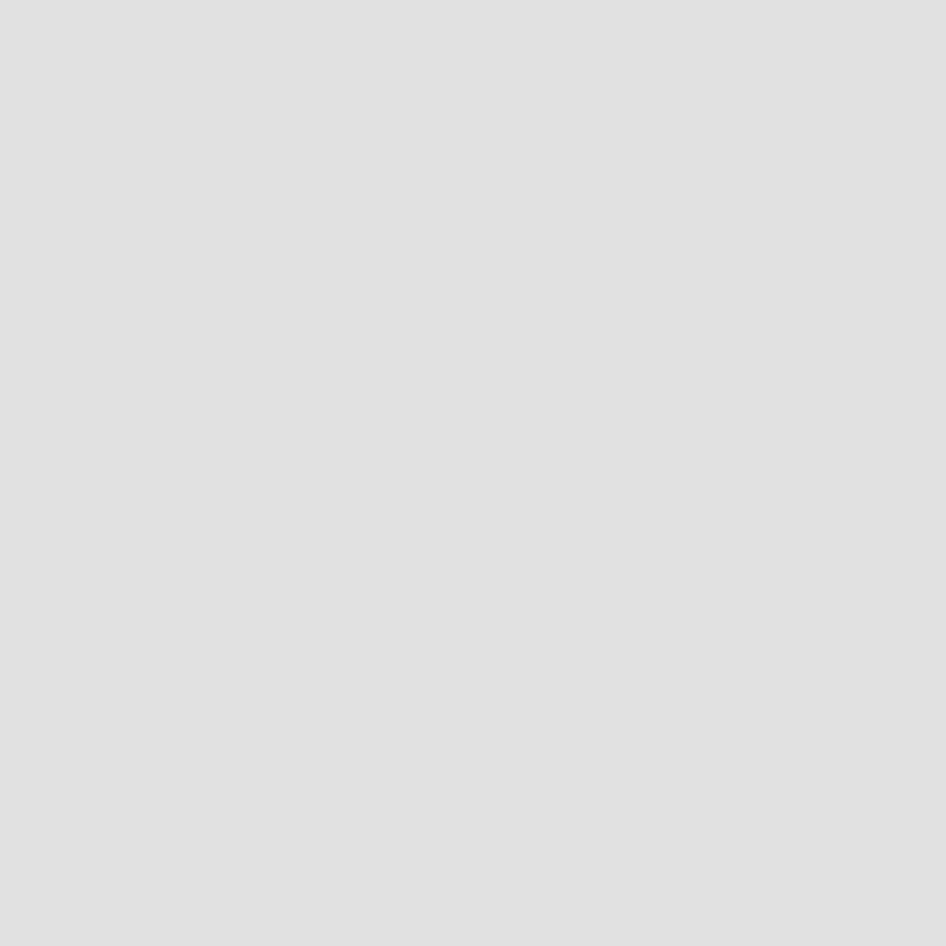
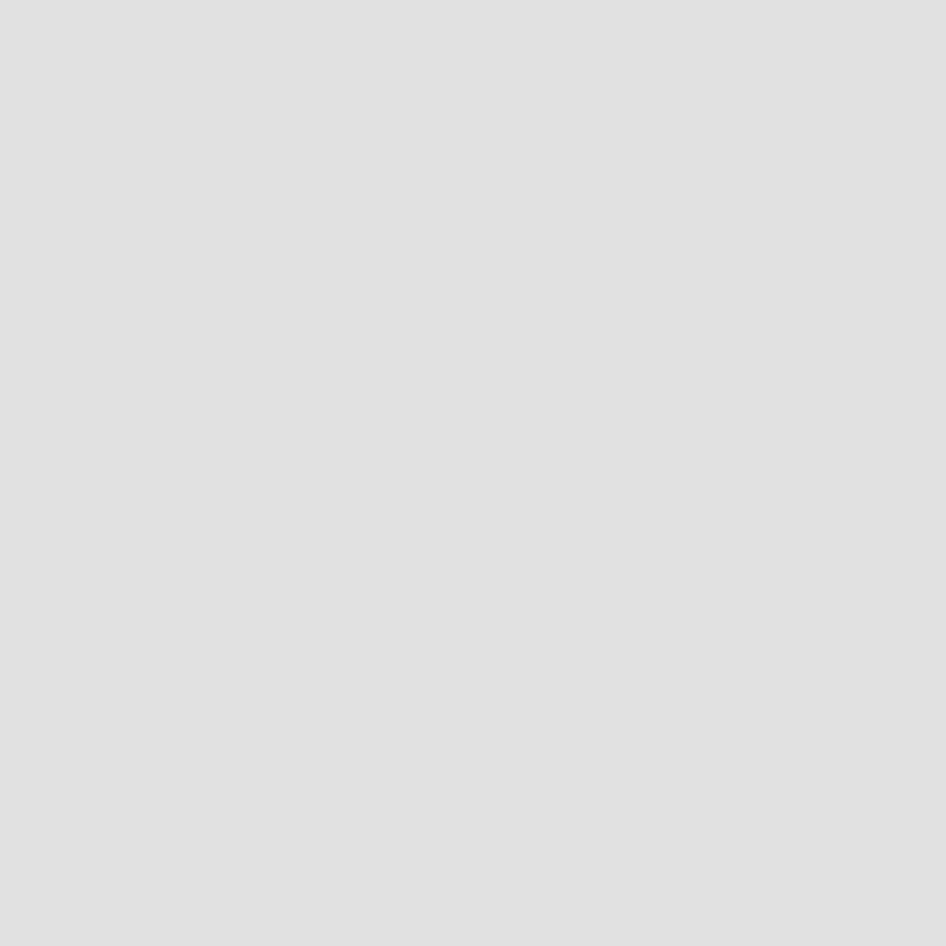
Which Vertical Conveyor Is Best for Your Operations?
Joe Joice
March 26, 2017
To keep pace with consumer expectations and enable direct-to-consumer delivery, retailers and manufacturers are rapidly evolving their distribution center strategies. Many are migrating their fulfillment operations toward mega-cities and high-population centers to enable on-time delivery, making the efficiency of these DCs more important than ever. But things are also evolving inside the four walls to maximize the available space and optimize product and employee workflows. This "warehousing compression" strategy requires better utilization of vertical spaces and new automation equipment to support this upward trend in high-density facilities.
Some innovative approaches to vertical expansion include facility upgrades to include mezzanines, multiple floors and, most importantly, vertical conveyors to facilitate the movement of product throughout these various levels. Whether it's footprint, flexibility, throughput or ergonomic consideration, each facility has different requirements for its vertical conveyors.
In Intelligrated's most recent On The Move webinar titled, "Vertical solutions: elevating your products to the next level," I discussed the available vertical conveyor options to meet these challenges. While the concept of vertical conveyance is relatively simple - moving product in a carton or tote to a different level in the warehouse - the variety of options to accomplish this can address varying degrees of process complexity. To select the best option for your operations, it's important to understand the pros and cons of each option.
As I presented in the webinar, vertical conveyors fall into four basic categories:
Continuous flow - Comprised of either incline or spiral options, continuous flow conveyors feature belt or motor-driven rollers and offer simple control systems. While incline conveyors provide high throughput rates, they are limited to single entry and exit points, and take up a lot of floor space. Similarly, spiral conveyors also provide high throughput rates and a relatively large footprint, but offer multiple entry and exit points.
Suspended shelf - As the name implies, suspended shelf conveyors employ a vertical shelf design to achieve multiple product elevations. Continuous suspended shelf options utilize a simple control system, provide single entry and exit points, offer medium throughput rates and still require medium to large space allotments.
Indexing suspended shelf - These servo-control systems have similar characteristics to suspended shelf conveyors while adding the benefits of multiple entry and exit points, and vertical merging and sorting.
Reciprocating conveyor - Vertical reciprocating conveyors (VRC) offer maximum flexibility in conveyor / shelving configurations and take up very little floor space. Also driven by a servo-control system, VRCs integrate with single-, double- or triple-zone conveyors; offer over- or under-conveyor configurations; and can be utilized in speciality zones such as transfers or turntables to deliver product to the most ergonomic position for workers. Since the shelf returns to the start position for product induction, VRCs operate at lower throughput rates. Regardless, the flexibility and small footprint of VRCs are making it an increasingly popular option.
Ultimately, selecting a vertical conveyor depends on your specific business objectives. To learn more about the possibilities of vertical conveyance and better understand which option is right for you, please view the webinars on our website.
To subscribe to our blog and receive exclusive communications and updates from Honeywell Intelligrated, click here.
Let's Connect!
Sign up to receive exclusive communications from Honeywell including product updates, technical information, new offerings, events and news, surveys, special offers, and related topics via telephone, email, and other forms of electronic communication.
Copyright © 2025 Honeywell International Inc
Maximum File Size
Maximum Files Exceeded
Due to inactivity you will be logged out in 000 seconds.
Maximum File Size
Maximum Files Exceeded
You cannot access this page as this product is not available in your country.