-
Global
-
Africa
-
Asia Pacific
-
Europe
-
Latin America
-
Middle East
-
North America
- |
- Partners
- |
- Blog
- |
- Contact Us
- |
-
Services
Services
-
Productivity
Productivity -
Safety
Safety -
Warehouse Automation
Warehouse Automation
-
-
Industries
Industries
-
Healthcare and Life Sciences
Healthcare and Life Sciences -
Transportation and Logistics
Transportation and Logistics -
Manufacturing
Manufacturing -
Distribution Centers
-
Retail
Retail -
E-Commerce
-
Infrastructure
Infrastructure -
Government
Government -
Aerospace and Defense
-
Electrification
-
-
Support
Support
-
Productivity
Productivity -
Safety
Safety -
Sensing Solutions
Sensing Solutions-
Training
-
Sales Contact Form
-
Technical Support
-
Certificates
-
eCOM Portal
-
Distributor Inventory
-
Blog
-
Return Material Authorization (Test & Measurement)
-
Return Material Authorization (Citytech)
-
Return Material Authorization (EnviteC)
-
Legal Documents
-
Return Material Authorization (ILC)
-
Intelligent Life Care
-
-
Warehouse Automation
Warehouse Automation -
Global Tracking
Global Tracking
-
-
Where to Buy
Where to Buy
You are browsing the product catalog for
Counter Uncertainty with Predictability Through Connected Services
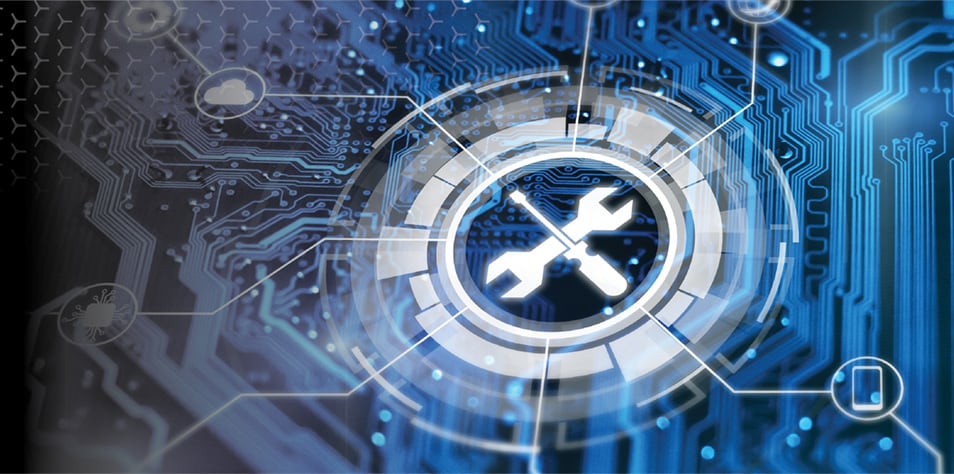
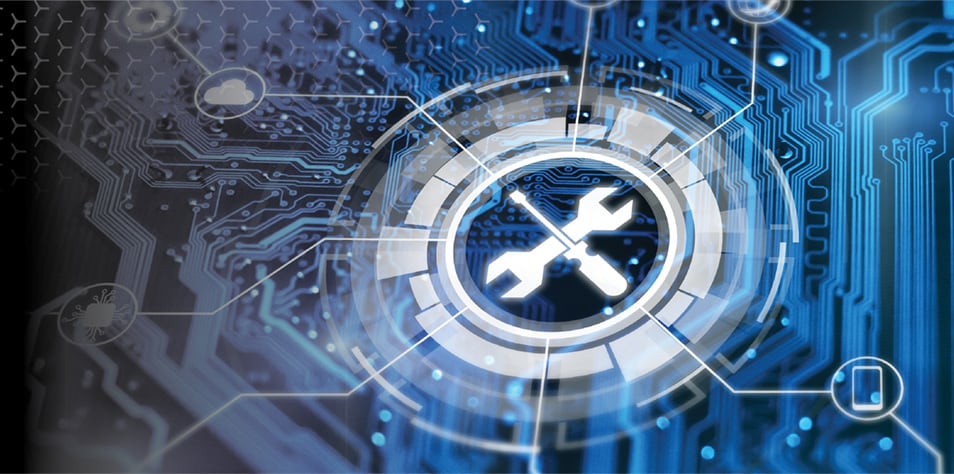
Counter Uncertainty with Predictability Through Connected Services
Eric Rice
April 14, 2021
The 2020 pandemic has driven many companies to move past piloting the integration of industrial internet of things (IIoT) technologies into their distribution and fulfillment (D&F) maintenance and operations (M&O) and into actual implementation. That’s because one of the biggest maintenance challenges in the current D&F environment is avoiding unplanned downtime.
With key equipment and assets ever more important and essential, the costs associated with downtime have risen significantly. How much? Up to 80 percent of organizations aren’t even sure, with many underestimating those costs by as much as 300 percent. Not only does that uncertainty make recovery from downtime much more difficult, it contributes to missed service level agreements (SLAs), damaged brand reputation and lost customer loyalty.
The answer? Connected services for M&O lifecycle management. By leveraging IIoT-connected assets via sensors and control system data, operations that require near-100 percent uptime can keep their key material handling equipment (MHE) running at the rates needed to keep pace with consumer demands.
The Value of Predictive Programs
Most companies operate without objective baseline data about the current health of their essential MHE. Understanding the intricacies of these systems typically falls within the purview of veteran technician staff members, who evaluate system condition by “feel” and whose insights are mostly undocumented or considered tribal knowledge.
The conversion of actual operational data into business value was studied by the Department of Energy (DOE) more than a decade ago. The ensuing report documented how the use of data in functional predictive maintenance programs delivers multiple benefits, including:
- 10X return on investment
- 25–30 percent reduction in maintenance costs
- 70–75 percent elimination of equipment breakdowns
- 35–40 percent decrease in downtime needed to perform maintenance
- 20–25 percent increase in production
Partnering for Improved Connectivity
In the midst of tackling the day-to-day challenges posed by COVID-19, most companies realize they are not equipped to manage IIoT initiatives on their own. Therefore, many are choosing to partner with an experienced lifecycle management service provider to help them:
- Define the scope and desired outcomes of the initiatives
- Extract the benefits of a connected M&O strategy
- Interpret data into actionable insights
- Provide coaching on IIoT adoption
- Hold internal stakeholders accountable for action items
Considering the diversity of D&F operations, a one-size-fits-all approach to lifecycle management isn’t realistic. Instead, a connected services partner can provide a framework for flexible commercial lifecycle management agreements that align with a company’s financial preferences and operational constraints.
Rather than incurring large intermittent expenses — typically from resolving major downtime issues — a partner can offer more predictable financial arrangements that may even flex with seasonal demand fluctuations and profit margins. Further, an experienced lifecycle management partner can help an operation evaluate its strengths and weaknesses and develop programs tailored to its preferences and business goals.
To learn more about how Honeywell Intelligrated can help you transition to a more predictive lifecycle management program — lowering your labor costs, increasing system reliability and uptime, and maximizing the utilization of your operations to meet current and future demands — read this On The Move article.
To subscribe to our blog and receive exclusive communications and updates from Honeywell Intelligrated, click here.
Let's Connect!
Sign up to receive exclusive communications from Honeywell including product updates, technical information, new offerings, events and news, surveys, special offers, and related topics via telephone, email, and other forms of electronic communication.
Copyright © 2024 Honeywell International Inc
Maximum File Size
Maximum Files Exceeded
Due to inactivity you will be logged out in 000 seconds.