-
Global
-
Africa
-
Asia Pacific
-
Europe
-
Latin America
-
Middle East
-
North America
- |
- Partners
- |
- Blog
- |
- Contact Us
- |
-
Services
Services
-
Productivity
Productivity -
Safety
Safety -
Warehouse Automation
Warehouse Automation
-
-
Industries
Industries
-
Healthcare and Life Sciences
Healthcare and Life Sciences -
Transportation and Logistics
Transportation and Logistics -
Manufacturing
Manufacturing -
Distribution Centers
-
Retail
Retail -
E-Commerce
-
Infrastructure
Infrastructure -
Government
Government -
Aerospace and Defense
-
Electrification
-
-
Support
Support
-
Productivity
Productivity -
Safety
Safety -
Sensing Solutions
Sensing Solutions-
Training
-
Sales Contact Form
-
Technical Support
-
Certificates
-
eCOM Portal
-
Distributor Inventory
-
Blog
-
Return Material Authorization (Test & Measurement)
-
Return Material Authorization (Citytech)
-
Return Material Authorization (EnviteC)
-
Legal Documents
-
Return Material Authorization (ILC)
-
Intelligent Life Care
-
-
Warehouse Automation
Warehouse Automation -
Global Tracking
Global Tracking
-
-
Where to Buy
Where to Buy
You are browsing the product catalog for
Seven Ways Stocking Critical Spare Parts Can Keep Your DC Operating Smoothly
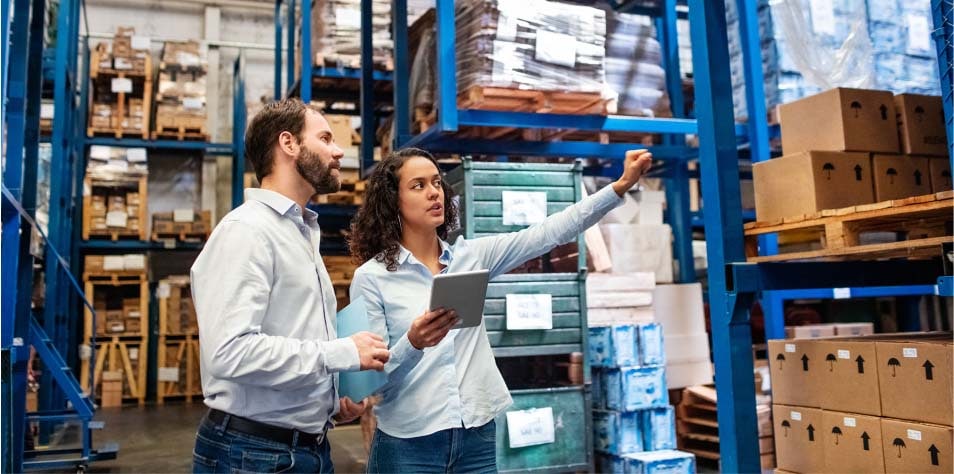
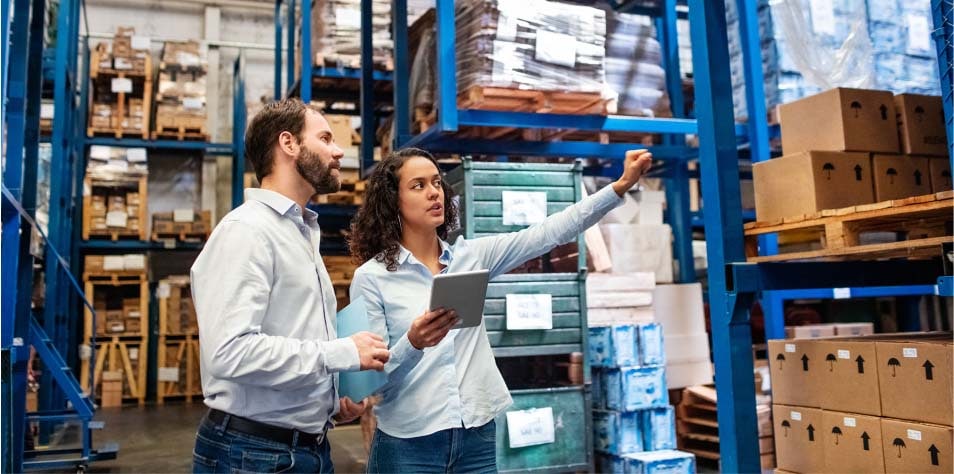
Seven Ways Stocking Critical Spare Parts Can Keep Your DC Operating Smoothly
Cindy Lyneis
July 27, 2021
Seven Ways Stocking Critical Spare Parts Can Keep Your DC Operating Smoothly
What’s the single most important — yet easiest — step you can take to prevent unexpected downtime in a distribution center (DC) or warehouse?
Stocking critical spare parts for advanced automated material handling equipment (MHE) on-site.
Having the right parts at the right time can keep DCs running at peak performance and make the greatest impact upon productivity. And since about 50 percent of all maintenance, repair and operations (MRO) budgets are spent on spare parts, the manner by which you identify, purchase and store the replacements also can influence how much DC operations contribute to achieving your organization’s financial objectives.
Not all manufacturers, retailers or logistics providers are well prepared with MHE spare parts in inventory to support appropriate preventive maintenance (PM) programs — let alone to handle equipment failure that disrupts operations. To reduce the risks, here are seven steps you can take to expedite planned maintenance and prevent prolonged, unexpected outages.
1. Establish a System to Track Warehouse Parts Inventory
Utilize computerized maintenance management systems (CMMS) and/or enterprise asset management systems (EAMS) to manage parts inventories and provisioning. DC operators who do not have one of these systems in place can set up a simple Excel spreadsheet to implement processes for the check-in/check-out of spare parts.
These records should list all part numbers and descriptions, vendor(s), lead time, quantity that should be on hand and the quantity actually on hand.
We recommend this as your first step. According to the Federal Energy Management Program, using a CMMS can:
- Increase maintenance productivity by more than 28 percent
- Reduce equipment downtime by 20 percent
- Lower expenses for material costs by more than 19 percent
2. Ask OEMs to List Recommended Spare Parts
Rely on recommended spare parts lists from the original equipment manufacturer (OEM) of your MHE and systems. OEMs provide a comprehensive list of all the parts you’ll need on-site.
In addition to providing a snapshot of on-hand inventory, a thorough analysis should identify the most up-to-date part numbers, the criticality of each part, lead time needed to replenish individual parts, and information about whether the part is obsolete (and if the OEM has recommended a substitute).
3. Estimate and Budget for Realistic Parts Costs
As MHE ages, spare parts expenses can increase. To better manage those costs, conduct an annual assessment of your equipment and systems to determine what maintenance is required, what parts are needed, and whether upgrades are available. These steps can enable you to prepare an accurate annual spare parts budget.
Be sure to review historical information from your CMMS as well as consult with the MHE OEM. Ask for recommendations for scheduled maintenance as well as spare parts that can be predicted based on the age of the equipment, your application and other performance factors.
4. Organize How Parts Are Stored
Finding the spare parts when you need them most requires setting up and maintaining a well-organized spare parts cage. Keep your storage area clean, secure, and labeled with location IDs and part numbers corresponding to records within your asset management system.
Standardize parts storage organization and processes across your enterprise to make it easier for teams to work across locations, including establishing universal procedures for tracking parts ordered, parts received and parts checked out of the spare parts cage.
5. Regularly Update On-Site Inventory
Inventory needs to be accurately tracked. Maintenance teams should perform annual physical inventory or institute periodic cycle counts to make sure critical MHE parts are on-site. Establishing a system of visual cues will help to make identifying critical parts easier. Regular checks also enable you to identify opportunities to consolidate parts or reduce quantities in inventory based on usage.
In addition, set up methods for maintenance technicians to tell you what parts they used and what ones they need.
6. Choose Trusted Vendors, Not Lowest-Cost Parts
It’s tempting to choose vendors offering the lowest cost for generic spare parts. But before you do, ask the vendor if they will help you to plan for emergencies, enable you to prepare an accurate spare parts budget, and stay up to date about alternatives for obsolescent parts.
If your operations go down in the middle of the night, how quickly can the vendor ship critical parts? Also, will using generic parts jeopardize warranty compliance?
To keep systems running smoothly and avoid unplanned outages, work with a trusted vendor to set up and maintain a well-stocked inventory of OEM-engineered replacement parts intended to perform with your equipment and applications. OEMs offer live parts assistance, with expert advisers available by phone or email on weekdays and on a 24/7 emergency basis to order parts. Many OEMs also provide an easy-to-use online store with up-to-date information about parts availability, your complete order history and access to the parts you need.
7. Thoroughly Train Maintenance Teams
Ensure that maintenance technicians are knowledgeable about your MHE and systems by providing proper training to document maintenance and repair procedures and reinforce best practices. Preparing the technicians to respond when unplanned downtime occurs — including knowing what spare parts are needed, what parts are in inventory, and how to locate them on-site or from your OEM vendor — is the key to minimizing costs and delays in operations.
Thorough training in spare parts inventory and parts management practices also should be a part of the onboarding for every newly hired maintenance technician.
Invest to Minimize Unplanned Downtime and Costs
Investing in an on-site inventory of OEM spare parts — combined with a proactive and well-organized maintenance program — can enable DC operators to minimize the costs of unplanned downtime. You will always know which critical parts are available, where they’re located, and have well-trained technicians ready to perform scheduled maintenance as well as emergency repairs. In addition, establishing, standardizing and maintaining an on-site inventory can improve productivity and reduce overall warehouse maintenance costs.
To subscribe to our blog and receive exclusive communications and updates from Honeywell Intelligrated, click here.
Let's Connect!
Sign up to receive exclusive communications from Honeywell including product updates, technical information, new offerings, events and news, surveys, special offers, and related topics via telephone, email, and other forms of electronic communication.
Copyright © 2024 Honeywell International Inc
Maximum File Size
Maximum Files Exceeded
Due to inactivity you will be logged out in 000 seconds.