-
Global
-
Africa
-
Asia Pacific
-
Europe
-
Latin America
-
Middle East
-
North America
- |
- Partners
- |
- Blog
- |
- Contact Us
- |
-
Services
Services
-
Productivity
Productivity -
Safety
Safety -
Warehouse Automation
Warehouse Automation
-
-
Industries
Industries
-
Healthcare and Life Sciences
Healthcare and Life Sciences -
Transportation and Logistics
Transportation and Logistics -
Manufacturing
Manufacturing -
Distribution Centers
-
Retail
Retail -
E-Commerce
-
Infrastructure
Infrastructure -
Government
Government -
Aerospace and Defense
-
Electrification
-
-
Support
Support
-
Productivity
Productivity -
Safety
Safety -
Sensing Solutions
Sensing Solutions-
Training
-
Sales Contact Form
-
Technical Support
-
Certificates
-
eCOM Portal
-
Distributor Inventory
-
Blog
-
Return Material Authorization (Test & Measurement)
-
Return Material Authorization (Citytech)
-
Return Material Authorization (EnviteC)
-
Legal Documents
-
Return Material Authorization (ILC)
-
Intelligent Life Care
-
-
Warehouse Automation
Warehouse Automation -
Global Tracking
Global Tracking
-
-
Where to Buy
Where to Buy
You are browsing the product catalog for
Is Your WMS Aligned to Address Your Warehouse Workflows?
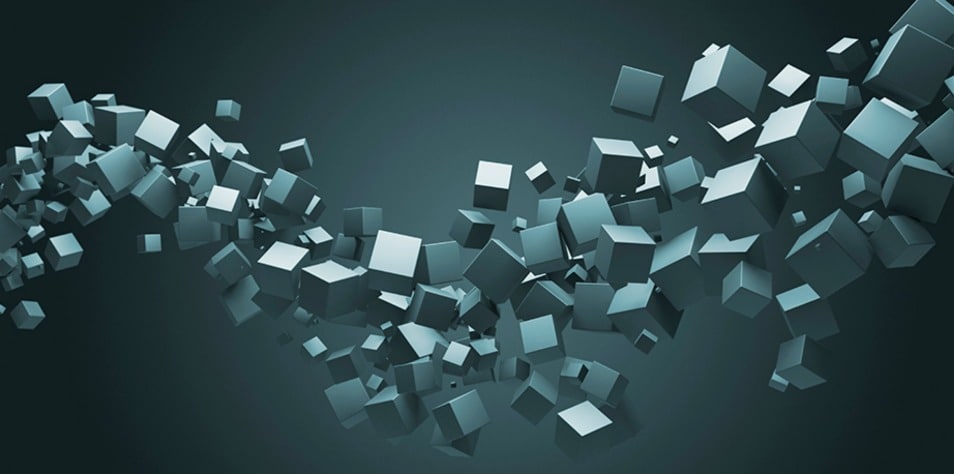
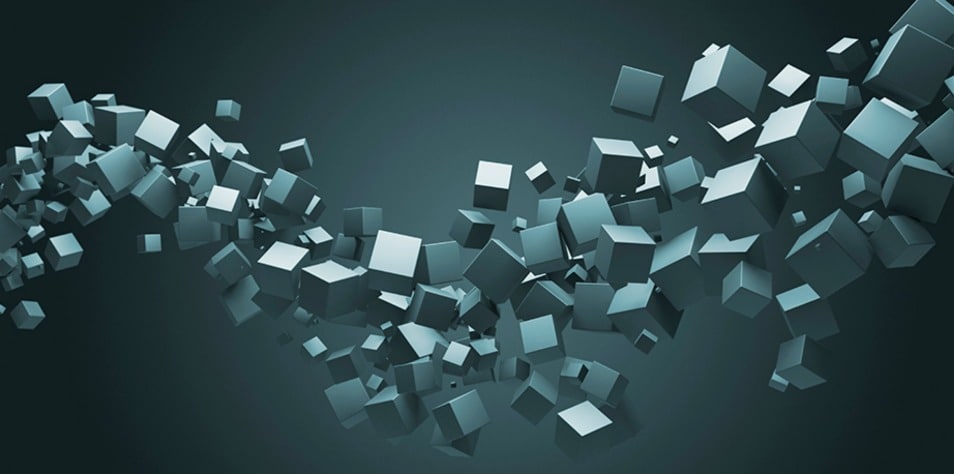
Is Your WMS Aligned to Address Your Warehouse Workflows?
Elisaveta Dimova
April 8, 2021
In most distribution centers (DCs) that are dedicated to e-commerce and omnichannel fulfillment, warehouse management systems (WMS) have become integral parts of their technological ecosystems. A WMS typically enables connection to an enterprise resource planning (ERP) system and/or an order management system (OMS) — a necessary component for bringing purchase orders and sales orders into warehouse workflows.
Inventory inaccuracies in distribution and fulfillment (D&F) operations can lead to a variety of issues that impact customer service levels (SLAs) and erode profit margins. A well-integrated WMS serves a variety of end-to-end inventory management and order fulfillment functions that can help to drive improved accuracy levels:
- Receiving and putting away inventory from inbound purchase orders
- Managing inventory quantity and location instructions within the four walls
- Creating waves of outbound sales orders that allocate inventory and generate picking tasks which are released to the floor for fulfillment execution
- Providing real-time inventory and status information during these activities
When combined with a warehouse execution system (WES), a WMS provides a crucial link between incoming orders and the ability to leverage more advanced fulfillment execution and automation.
But in the search for a best-fit WMS, many operations struggle to find a solution that aligns with their unique workflows, processes and business goals. As is often the case, companies either invest in an all-or-nothing approach with more features than they will ever use or develop a homegrown system that they quickly outgrow while it continues to consume precious internal resources.
In the fast-paced and intensely demanding e-commerce marketplace, D&F operations develop unique workflows to address their own specific fulfillment requirements and customer SLAs. It’s a dynamic environment where priorities shift quickly, business requirements change, and processes evolve. To succeed, operations need a WMS that has the flexibility to adapt with these changes.
A highly configurable WMS alternative
In response to these all-too-common challenges, Honeywell Intelligrated is alleviating these issues by introducing: Momentum WMS. With more than 500 control parameters that can be activated or deactivated with the click of a button, Momentum WMS allows you to precisely configure its functionality to your specific warehouse workflows — without over-investing or incurring the time and expense of custom coding.
Momentum WMS is designed to support a variety of industries and D&F operations, such as: pharmaceutical, e-commerce, apparel, cold chain, third-party logistics (3PL), manufacturing and retail. From inbound receipt and order fulfillment processing to replenishment and outbound distribution, Momentum WMS seamlessly integrates into a variety of workflows and key warehouse functions:
- ERP and/or host system integration
- Inventory receiving and replenishment
- Real-time inventory tracking
- Order fulfillment
- Label printing
- Packaging and shipping
- Reporting and dashboard
- Transportation management integration
- Distributed order management integration
Reliable platform delivers lasting benefits
Momentum WMS is built to deliver industry-leading reliability within an advanced and user-friendly interface. It leverages a powerful, stable and modular ecosystem that allows end users to easily activate features and functionalities as needed. This platform empowers Momentum WMS to deliver seamless integration with your warehouse automation infrastructure — whether your business rules change, you add new material handling equipment (MHE), or need to connect to other external systems.
With Momentum WMS, you’ll get the robust tools you need to transform your operations today while providing the flexibility to adapt to evolving business requirements for years to come:
- Fast to install and implement
- Deep configurability with warehouse operations and workflows
- Easily expandable to adapt to future business changes
- Capable of integrating with other warehouse automation software
For more information on how Momentum WMS can give your business the flexible, end-to-end control you need to streamline your inventory management and order fulfillment operations, view our white paper.
To subscribe to our blog and receive exclusive communications and updates from Honeywell Intelligrated, click here.
Let's Connect!
Sign up to receive exclusive communications from Honeywell including product updates, technical information, new offerings, events and news, surveys, special offers, and related topics via telephone, email, and other forms of electronic communication.
Copyright © 2024 Honeywell International Inc
Maximum File Size
Maximum Files Exceeded
Due to inactivity you will be logged out in 000 seconds.